Inventory management is one of the most complex challenges a company can face. Delivery delays, product shortages at critical times, or surpluses that take up space unnecessarily are just some of the most common issues caused by poor inventory management issues that can harm not only business operations but also the company’s reputation and image.
In an increasingly competitive market, adopting advanced strategies to optimize inventory and improve logistics is not just an option but a necessity. In this article, we’ll show you how to turn inventory management into a competitive advantage for your company.
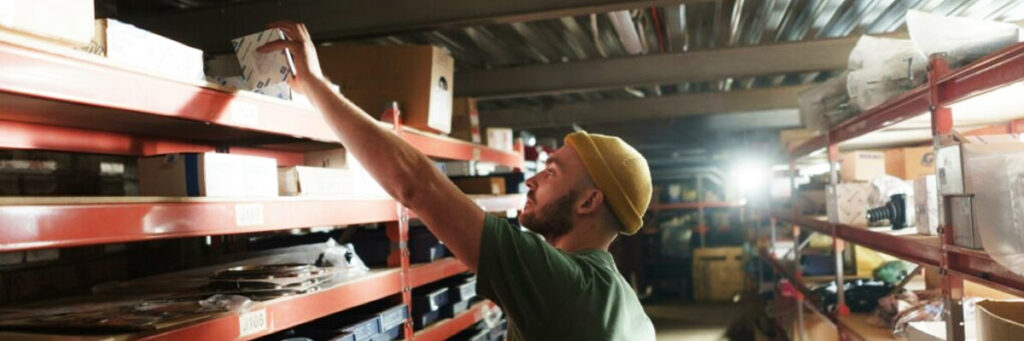
Why Effective Inventory Management is Crucial for Businesses
A well-organized inventory ensures an effective balance between supply and demand, cutting unnecessary costs and meeting customer expectations. Ensuring products are available at the right time not only reduces waste but also increases consumer trust.
Conversely, management errors can be costly: unnecessary warehouse expenses, spoiled products, and missed sales opportunities are just some of the consequences. Tools like predictive analytics software and automated systems can help prevent these issues, significantly improving business efficiency.
What Are the Costs of Inventory Management?
Inventory management involves significant costs, such as:
- Warehouse operating costs: rent, energy, and maintenance.
- Personnel costs: for handling and managing goods.
- Forecasting errors: leading to surplus or shortages.
- Obsolescence: unsold or spoiled products.
Optimizing these costs requires strategic planning and cutting-edge technologies. For instance, demand forecasting software helps plan targeted procurement, reducing expenses and improving profitability.
The Main Problems in Inventory Management
Ineffective inventory management can significantly impact business performance,negatively affecting operational costs, efficiency and customer satisfactionMany businesses struggle with accurately predicting product demand, managing structural issues in warehouse organization, and properly coordinating stock. If ignored, these challenges can result in unused surplus, unexpected shortages, and delays across the supply chain.
To ensure smooth and sustainable operations, it’s essential to recognize and address these obstacles with strategic approaches and suitable tools.
Demand Forecasting Errors
Accurately forecasting customer demand is not always easy. Incorrect estimates can lead to stock surplus, with unsold products taking up valuable warehouse space, or shortages that prevent timely fulfillment of customer requests, damaging trust and the company’s image.
These errors often stem from poor integration of data across departments, a lack of advanced analytical tools, or sudden changes in purchasing behavior. Implementing an integrated management system is essential to address these challenges. By analyzing real-time data, these tools can identify trends, anticipate demand fluctuations, and support more informed decision-making. This approach not only improves forecasting accuracy but also optimizes the entire supply chain.
Coordination Issues in Warehouse Logistics
Lack of coordination in logistics increases the risk of errors and waste of time and resources. For example, chaotic coordination or poor inventory traceability can make picking and storage slower and more complex, undermining overall efficiency and causing delivery delays.
Addressing these issues requires automation and space optimization. Advanced technologies, such as warehouse management systems, enhance processes by providing real-time inventory visibility and drastically reducing errors. Additionally, a smart layout of goods, with well-defined areas for storage, picking, and shipping, accelerates operations and streamlines workflows.
By implementing innovative solutions and investing in strategic warehouse management, businesses can transform what is often a critical point into a driver of efficiency and competitiveness.
Stock Management Problems
Inefficient stock management can lead to product shortages during demand peaks or, conversely, surplus stock occupying space unnecessarily. These imbalances compromise customer satisfaction and increase operational costs, such as storage expenses, waste management, or lost sales opportunities.
For example, a seasonal clothing retailer might face excess coats at the end of winter, tying up capital and warehouse space. Conversely, an electronics e-commerce platform might struggle to meet demand during Black Friday, losing potential customers due to insufficient stock.
Monitoring stock levels in real-time with advanced management software can make all the difference. These tools enable better demand prediction, timely restocking, and optimal inventory levels. For instance, a food company could use an integrated system to automatically reorder fresh products when quantities drop below a critical threshold, avoiding waste and ensuring availability for customers.
Adopting these solutions not only improves operational efficiency but also builds a more flexible and resilient supply chain capable of quickly responding to market changes.